Graxa para Lubrificação: 7 Dicas para Escolher a Ideal
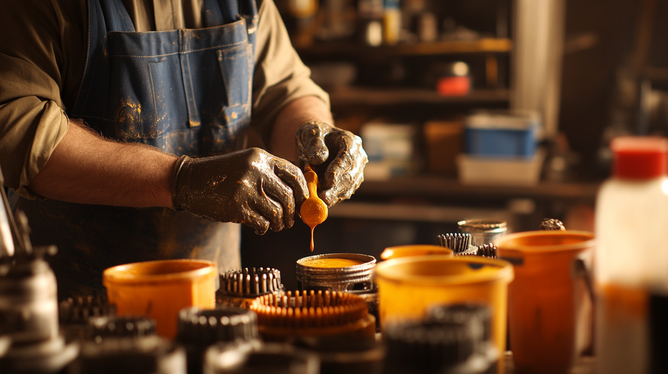
Por: Antonio - 21 de Dezembro de 2024
Graxa para lubrificação é um componente vital para o funcionamento adequado de máquinas e equipamentos. Neste artigo, vamos explorar os diferentes tipos de graxa, como escolher a mais adequada para suas necessidades e os benefícios que ela pode trazer. Continue lendo para descobrir dicas valiosas sobre aplicação e manutenção, garantindo assim a longevidade dos seus equipamentos.
Tipos de Graxa para Lubrificação
Existem diversos tipos de graxa para lubrificação, cada uma projetada para atender a necessidades específicas de diferentes aplicações. A escolha da graxa correta é fundamental para garantir a eficiência e a durabilidade de máquinas e equipamentos. Neste artigo, vamos detalhar os principais tipos de graxa disponíveis no mercado e suas características.
Uma das classificações mais comuns para graxas é baseada na base do lubrificante. As graxas podem ser divididas em três categorias principais: graxas à base de óleo mineral, graxas sintéticas e graxas à base de biolubrificantes. Cada uma delas possui propriedades únicas que as tornam adequadas para diferentes condições de operação.
A graxa à base de óleo lubrificante mineral é uma das mais utilizadas. Ela é composta por óleos minerais refinados e aditivos que melhoram suas propriedades de lubrificação. Essa graxa é ideal para aplicações em ambientes normais, onde não há grandes variações de temperatura ou pressão. Ela oferece boa proteção contra corrosão e desgaste, além de ter um custo acessível.
As graxas sintéticas, por outro lado, são formuladas a partir de compostos químicos artificiais. Elas são projetadas para oferecer desempenho superior em condições extremas, como altas temperaturas e pressões elevadas. As graxas sintéticas têm uma maior resistência à oxidação e à degradação, o que as torna ideais para aplicações em ambientes severos, como na indústria aeroespacial e automotiva. Além disso, elas tendem a ter uma vida útil mais longa em comparação com as graxas à base de óleo mineral.
Outro tipo importante de graxa é a graxa à base de biolubrificantes, que é feita a partir de óleos vegetais ou animais. Essas graxas são uma alternativa sustentável e ecológica, pois são biodegradáveis e menos prejudiciais ao meio ambiente. Elas são frequentemente utilizadas em aplicações onde a contaminação ambiental é uma preocupação, como na agricultura e na indústria de alimentos. Apesar de suas vantagens ambientais, as graxas à base de biolubrificantes podem ter limitações em termos de estabilidade e desempenho em altas temperaturas.
Além da base do lubrificante, as graxas também podem ser classificadas de acordo com o tipo de espessante utilizado. Os espessantes são substâncias que conferem à graxa sua consistência e propriedades de aderência. Os espessantes mais comuns incluem sabões de lítio, sabões de cálcio e argilas. As graxas à base de sabão de lítio são amplamente utilizadas devido à sua versatilidade e resistência à água, tornando-as adequadas para uma ampla gama de aplicações.
As graxas à base de sabão de cálcio, por sua vez, são conhecidas por sua excelente resistência à água, o que as torna ideais para ambientes úmidos e aquáticos. Elas são frequentemente utilizadas em equipamentos marítimos e em aplicações industriais onde a exposição à água é uma preocupação. As graxas de argila, embora menos comuns, são utilizadas em aplicações específicas que exigem alta resistência ao calor e à pressão.
Outro fator a considerar ao escolher a graxa para lubrificação é a viscosidade. A viscosidade é uma medida da resistência de um fluido ao fluxo e é um parâmetro crucial para o desempenho da graxa. Graxas com viscosidade mais alta tendem a oferecer melhor proteção em condições de carga pesada, enquanto graxas com viscosidade mais baixa são mais adequadas para aplicações de alta velocidade.
Além disso, é importante considerar a temperatura de operação ao escolher a graxa. Algumas graxas são projetadas para operar em temperaturas extremas, tanto altas quanto baixas. A escolha da graxa correta para a temperatura de operação específica pode ajudar a evitar falhas prematuras e garantir o desempenho ideal dos equipamentos.
Em resumo, a escolha do tipo de graxa para lubrificação deve ser baseada em uma análise cuidadosa das condições de operação, das características do equipamento e das necessidades específicas de cada aplicação. Compreender os diferentes tipos de graxas disponíveis no mercado e suas propriedades pode ajudar na seleção do produto mais adequado, garantindo assim a eficiência e a longevidade dos seus equipamentos.
Como Escolher a Graxa Ideal
Escolher a graxa ideal para lubrificação é um passo crucial para garantir o desempenho e a durabilidade de máquinas e equipamentos. Com tantas opções disponíveis no mercado, é fundamental entender os fatores que influenciam essa escolha. Neste artigo, abordaremos os principais aspectos a serem considerados ao selecionar a graxa mais adequada para suas necessidades.
O primeiro fator a ser considerado é o tipo de equipamento que será lubrificado. Cada máquina ou componente pode ter requisitos específicos de lubrificação, dependendo de sua função e das condições em que opera. Por exemplo, equipamentos que operam em ambientes severos, como altas temperaturas ou pressão, podem exigir graxas sintéticas que oferecem melhor desempenho nessas condições. Já para aplicações mais simples, uma graxa à base de óleo mineral lubrificante pode ser suficiente.
Outro aspecto importante é a viscosidade da graxa. A viscosidade é uma medida da resistência de um fluido ao fluxo e pode afetar diretamente a capacidade de lubrificação. Graxas com viscosidade mais alta são geralmente mais eficazes em condições de carga pesada, pois conseguem suportar melhor as pressões e o atrito. Por outro lado, graxas com viscosidade mais baixa são mais adequadas para aplicações de alta velocidade, onde a fluidez é essencial. É importante consultar as especificações do fabricante do equipamento para determinar a viscosidade recomendada.
A temperatura de operação também desempenha um papel fundamental na escolha da graxa. Cada tipo de graxa tem uma faixa de temperatura em que funciona de maneira ideal. Graxas que não são adequadas para altas temperaturas podem se degradar rapidamente, resultando em falhas na lubrificação e danos ao equipamento. Por outro lado, graxas que não suportam baixas temperaturas podem se tornar muito viscosas, dificultando a movimentação das partes móveis. Portanto, é essencial escolher uma graxa que seja adequada para a faixa de temperatura específica em que o equipamento opera.
Além disso, a resistência à água é outro fator a ser considerado. Equipamentos que operam em ambientes úmidos ou que estão expostos à água frequentemente precisam de graxas que ofereçam excelente resistência à umidade. Graxas à base de sabão de cálcio, por exemplo, são conhecidas por sua capacidade de repelir a água, tornando-as ideais para aplicações em ambientes aquáticos. Já para ambientes secos, a resistência à poeira e sujeira pode ser mais relevante, e nesse caso, graxas com propriedades de adesão podem ser mais eficazes.
Os aditivos presentes na graxa também são um ponto importante a ser considerado. Os aditivos podem melhorar diversas características da graxa, como resistência à oxidação, proteção contra corrosão e capacidade de suportar cargas extremas. É importante escolher uma graxa que contenha os aditivos necessários para atender às exigências específicas do equipamento. Por exemplo, se um equipamento estiver sujeito a altas cargas, uma graxa com aditivos EP (extrema pressão) pode ser necessária para garantir a proteção adequada.
A frequência de lubrificação também deve ser levada em conta. Equipamentos que operam em condições severas podem exigir lubrificação mais frequente, enquanto outros podem necessitar de intervalos mais longos. A escolha da graxa ideal deve levar em consideração a durabilidade e a resistência à degradação, garantindo que a graxa mantenha suas propriedades ao longo do tempo. Graxas sintéticas, por exemplo, costumam ter uma vida útil mais longa, o que pode ser vantajoso em aplicações que exigem menos manutenção.
Por fim, é sempre recomendável consultar o manual do fabricante do equipamento para obter informações específicas sobre as recomendações de lubrificação. O fabricante pode fornecer orientações sobre o tipo de graxa, viscosidade e intervalos de lubrificação, ajudando a garantir que o equipamento opere de maneira eficiente e segura.
Em resumo, escolher a graxa ideal envolve considerar diversos fatores, como o tipo de equipamento, viscosidade, temperatura de operação, resistência à água, aditivos e frequência de lubrificação. Compreender essas variáveis permitirá que você faça uma escolha informada, garantindo a proteção e o desempenho adequado dos seus equipamentos. Ao seguir essas diretrizes, você poderá maximizar a eficiência operacional e prolongar a vida útil das máquinas, resultando em menos paradas e custos de manutenção. Portanto, dedique tempo para avaliar suas opções e selecione a graxa que melhor atenda às suas necessidades específicas.
Benefícios da Graxa para Lubrificação
A graxa para lubrificação desempenha um papel crucial na manutenção e operação de máquinas e equipamentos. Sua aplicação adequada pode resultar em diversos benefícios que impactam diretamente na eficiência e na durabilidade dos componentes mecânicos. Neste artigo, vamos explorar os principais benefícios da graxa para lubrificação e como ela pode contribuir para o desempenho ideal dos equipamentos.
Um dos principais benefícios da graxa é a redução do atrito entre as superfícies móveis. Quando as partes de uma máquina se movem, o atrito pode gerar calor e desgaste, levando a falhas prematuras. A graxa atua como uma barreira lubrificante, minimizando o contato direto entre as superfícies e, portanto, reduzindo o atrito. Isso não só prolonga a vida útil dos componentes, mas também melhora a eficiência operacional, já que menos energia é perdida na forma de calor.
Além da redução do atrito, a graxa também ajuda a prevenir a corrosão e o desgaste das peças. A maioria das graxas contém aditivos que protegem as superfícies metálicas contra a oxidação e a corrosão, que podem ser causadas pela umidade e outros contaminantes. Isso é especialmente importante em ambientes industriais, onde as máquinas estão expostas a condições adversas. Uma graxa de qualidade pode criar uma película protetora que impede a formação de ferrugem e corrosão, garantindo que os equipamentos mantenham seu desempenho ao longo do tempo.
A graxa também desempenha um papel importante na vedação contra contaminantes. Em muitas aplicações, poeira, sujeira e umidade podem entrar em contato com as partes móveis, causando danos e reduzindo a eficiência. A graxa atua como um vedante, formando uma barreira que impede a entrada desses contaminantes. Isso é especialmente relevante em ambientes onde a exposição a partículas sólidas é uma preocupação. A utilização de graxa adequada pode ajudar a manter os componentes limpos e operacionais, reduzindo a necessidade de manutenção frequente.
Outro benefício significativo da graxa para lubrificação é a capacidade de suportar altas cargas. Muitas graxas são formuladas com aditivos que melhoram sua resistência a cargas extremas, permitindo que suportem pressões elevadas sem se degradar. Isso é essencial em aplicações industriais, onde as máquinas estão frequentemente sujeitas a cargas pesadas. A escolha da graxa correta para cada aplicação pode ajudar a evitar falhas e quebras, resultando em menos paradas e custos de manutenção.
Além disso, a graxa para lubrificação pode melhorar a eficiência energética dos equipamentos. Quando as partes móveis estão bem lubrificadas, a resistência ao movimento é reduzida, permitindo que os motores e outros componentes operem com maior eficiência. Isso não só economiza energia, mas também diminui os custos operacionais a longo prazo. Em um ambiente industrial, onde o consumo de energia pode ser significativo, a escolha da graxa correta pode ter um impacto positivo nos custos gerais da operação.
A aplicação de graxa também contribui para a estabilidade térmica dos componentes. Graxas de alta qualidade são formuladas para suportar uma ampla faixa de temperaturas, garantindo que mantenham suas propriedades lubrificantes mesmo em condições extremas. Isso é vital em aplicações onde as máquinas operam em altas temperaturas, como em processos de usinagem. O uso de um Óleo solúvel para usinagem que seja compatível com as necessidades do equipamento pode ajudar a evitar o superaquecimento e a degradação dos componentes, garantindo um desempenho consistente e confiável.
Outro aspecto importante é a facilidade de aplicação e manutenção. A graxa é geralmente mais fácil de aplicar do que os óleos líquidos, pois sua consistência permite que ela permaneça no lugar, oferecendo uma lubrificação contínua por mais tempo. Isso significa que os intervalos de lubrificação podem ser mais longos, reduzindo a necessidade de manutenção frequente e permitindo que os operadores se concentrem em outras tarefas. A graxa também pode ser aplicada em locais de difícil acesso, onde a aplicação de óleo seria complicada.
Por último, mas não menos importante, a graxa para lubrificação pode contribuir para a sustentabilidade das operações. Ao prolongar a vida útil dos equipamentos e reduzir a necessidade de manutenção, a graxa ajuda a minimizar o desperdício de recursos e a reduzir a produção de resíduos. A utilização de graxas biodegradáveis e sustentáveis também pode ser uma opção viável para empresas que buscam reduzir seu impacto ambiental.
Em resumo, os benefícios da graxa para lubrificação são vastos e impactam diretamente no desempenho e na durabilidade dos equipamentos. Desde a redução do atrito e proteção contra corrosão até a melhoria da eficiência energética e a facilidade de aplicação, a graxa é um componente essencial para a manutenção adequada de máquinas e equipamentos. Ao escolher a graxa certa para cada aplicação, é possível maximizar a eficiência operacional e prolongar a vida útil dos componentes, resultando em menos paradas e custos de manutenção a longo prazo.
Dicas de Aplicação e Manutenção
A aplicação e a manutenção adequadas da graxa para lubrificação são fundamentais para garantir o desempenho ideal dos equipamentos e prolongar sua vida útil. Neste artigo, apresentamos dicas valiosas que ajudarão você a aplicar a graxa corretamente e a manter seus sistemas lubrificados em condições ideais. Seguir essas orientações pode resultar em menos falhas, maior eficiência e, consequentemente, economia nos custos operacionais.
Um dos primeiros passos para uma aplicação eficaz da graxa é conhecer o tipo de graxa que melhor se adapta ao seu equipamento. Cada máquina pode ter requisitos específicos de lubrificação, dependendo de fatores como carga, temperatura e ambiente de operação. Por isso, é essencial consultar o manual do fabricante para entender as recomendações sobre o tipo de graxa e a frequência de aplicação. A escolha errada da graxa pode levar a problemas de desempenho e até mesmo a danos irreparáveis.
Antes de aplicar a graxa, é importante preparar adequadamente a superfície a ser lubrificada. Isso significa limpar a área para remover sujeira, poeira e resíduos de graxa antiga. A presença de contaminantes pode comprometer a eficácia da nova lubrificação. Utilize um pano limpo e, se necessário, solventes apropriados para garantir que a superfície esteja livre de impurezas. Essa limpeza inicial ajuda a garantir que a nova graxa possa aderir corretamente e desempenhar suas funções de forma eficaz.
Ao aplicar a graxa, é importante utilizar a quantidade correta. Aplicar graxa em excesso pode causar problemas, como o acúmulo de resíduos, que podem levar ao superaquecimento e à falha do equipamento. Por outro lado, a aplicação insuficiente pode resultar em falta de lubrificação, aumentando o atrito e o desgaste. Utilize ferramentas adequadas, como pistolas de graxa, que permitem uma aplicação precisa e controlada. Siga as recomendações do fabricante sobre a quantidade exata a ser aplicada em cada componente.
Outro ponto a ser considerado é a frequência de aplicação. A lubrificação regular é vital para garantir que os componentes móveis estejam sempre protegidos. O intervalo entre as aplicações pode variar dependendo do tipo de equipamento, das condições de operação e do tipo de graxa utilizada. Em ambientes severos, onde há maior desgaste e contaminação, pode ser necessário lubrificar com mais frequência. Monitore o desempenho do equipamento e ajuste a frequência de aplicação conforme necessário.
Além disso, é importante verificar se a graxa utilizada é compatível com os materiais do equipamento. Algumas graxas podem reagir negativamente com certos materiais, causando degradação ou falha. Isso é especialmente relevante em aplicações que envolvem vedantes ou componentes plásticos. Consulte sempre as especificações do fabricante para garantir a compatibilidade da graxa com os materiais em uso.
Durante a manutenção, também é essencial inspecionar regularmente as condições dos componentes lubrificados. Verifique se há sinais de desgaste, corrosão ou falhas. A detecção precoce de problemas pode evitar falhas maiores e custos elevados de reparo. Se notar qualquer anomalia, tome providências imediatas para resolver a situação, seja ajustando a lubrificação ou substituindo peças danificadas.
Outro aspecto importante é a escolha do tipo de graxa em relação ao ambiente de operação. Para aplicações em ambientes úmidos ou expostos à água, considere o uso de graxas que ofereçam resistência à umidade. Graxas à base de sabão de cálcio, por exemplo, são conhecidas por sua capacidade de repelir a água, tornando-as ideais para esses cenários. Em contrapartida, para ambientes secos, graxas com propriedades de adesão podem ser mais eficazes.
Além da graxa, a escolha do óleo também deve ser considerada. Por exemplo, o óleo para compressor de ar é um componente essencial para a operação de compressores, e sua seleção deve ser feita com cuidado. Assim como a graxa, o óleo deve ser escolhido com base nas recomendações do fabricante e nas condições de operação do equipamento.
Por fim, é importante registrar as atividades de lubrificação e manutenção. Mantenha um registro detalhado das aplicações de graxa, incluindo datas, tipos de graxa utilizados e qualquer observação relevante sobre o desempenho do equipamento. Isso não apenas ajuda a manter um histórico de manutenção, mas também pode ser útil para identificar padrões e ajustar as práticas de lubrificação conforme necessário.
Em resumo, a aplicação e a manutenção adequadas da graxa para lubrificação são essenciais para o funcionamento eficiente dos equipamentos. Conhecer o tipo de graxa adequado, preparar corretamente as superfícies, aplicar a quantidade certa e manter um cronograma de lubrificação são passos fundamentais para garantir o desempenho ideal. Além disso, inspecionar regularmente os componentes e registrar as atividades de manutenção ajuda a prevenir problemas e a prolongar a vida útil dos equipamentos. Ao seguir essas dicas, você pode maximizar a eficiência operacional e minimizar os custos de manutenção, garantindo que suas máquinas funcionem de maneira confiável por muito mais tempo.
Em conclusão, a graxa para lubrificação desempenha um papel fundamental na manutenção e eficiência de máquinas e equipamentos. Ao compreender os diferentes tipos de graxa, suas características e como escolher a mais adequada, você pode garantir um desempenho ideal e uma vida útil prolongada para seus componentes. Além disso, aplicar as dicas de aplicação e manutenção discutidas neste artigo ajudará a evitar falhas e a reduzir custos operacionais. Portanto, invista tempo na seleção e na manutenção da graxa correta, pois isso resultará em operações mais suaves e confiáveis. Lembre-se de que a lubrificação adequada é um dos pilares para o sucesso na gestão de qualquer equipamento, e a atenção a esses detalhes fará toda a diferença no desempenho a longo prazo.