Graxa lubrificante: como escolher a melhor para suas necessidades
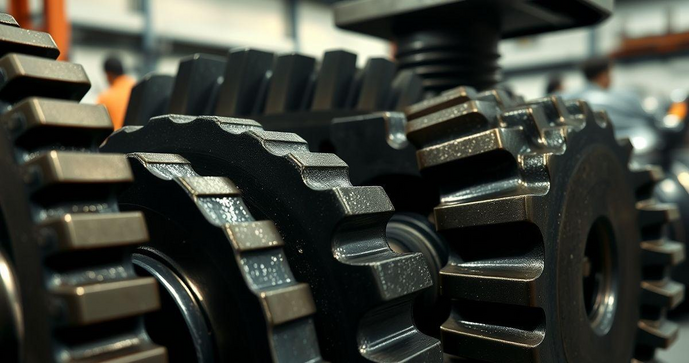
Por: Antonio - 22 de Fevereiro de 2025
A graxa lubrificante desempenha um papel crucial na manutenção e no funcionamento eficiente de máquinas e equipamentos. Ao reduzir o atrito e o desgaste, ela garante maior durabilidade e desempenho. Neste artigo, vamos explorar os diferentes tipos de graxa lubrificante, como escolher a mais adequada para suas necessidades e as vantagens de sua utilização, além de dicas para armazenamento e manutenção.
Tipos de Graxa Lubrificante e Suas Aplicações
A graxa lubrificante é um componente essencial em diversos setores industriais e em aplicações domésticas. Ela é utilizada para reduzir o atrito entre superfícies móveis, evitando o desgaste prematuro e aumentando a eficiência dos equipamentos. Existem diferentes tipos de graxa lubrificante, cada uma com características específicas que a tornam mais adequada para determinadas aplicações. A seguir, abordaremos os principais tipos de graxa lubrificante e suas respectivas utilizações.
Um dos tipos mais comuns de graxa lubrificante é a graxa à base de sabão. Essa categoria é amplamente utilizada em aplicações gerais, como em rolamentos, eixos e engrenagens. A graxa à base de sabão é composta por um espessante de sabão, que pode ser de lítio, cálcio ou sódio, misturado com um óleo base. A graxa de lítio, por exemplo, é conhecida por sua resistência à água e alta estabilidade térmica, tornando-a ideal para aplicações em ambientes úmidos e em altas temperaturas.
Outro tipo importante é a graxa sintética, que é formulada a partir de compostos químicos artificiais. Essa graxa oferece vantagens significativas em comparação com as graxas convencionais, como maior resistência à oxidação, melhor desempenho em temperaturas extremas e maior durabilidade. As graxas sintéticas são frequentemente utilizadas em aplicações críticas, como em motores de aeronaves, equipamentos de alta performance e em indústrias que exigem lubrificação confiável em condições severas.
A graxa de silicone é uma opção popular em aplicações que requerem resistência à água e propriedades de vedação. Ela é frequentemente utilizada em equipamentos elétricos, como conectores e interruptores, devido à sua capacidade de repelir a umidade e evitar a corrosão. Além disso, a graxa de silicone é inerte e não reage com a maioria dos materiais, o que a torna uma escolha segura para aplicações em que a compatibilidade é uma preocupação.
As graxas de alta temperatura são projetadas para suportar condições extremas de calor. Elas são formuladas com aditivos especiais que melhoram sua estabilidade térmica e resistência à degradação. Essas graxas são frequentemente utilizadas em aplicações industriais, como em fornos, turbinas e motores, onde as temperaturas podem ultrapassar os limites das graxas convencionais. A utilização de graxas de alta temperatura ajuda a garantir o funcionamento eficiente e seguro dos equipamentos, mesmo em condições adversas.
Além disso, existem graxas específicas para aplicações em ambientes agressivos, como a graxa resistente a produtos químicos. Essa graxa é formulada para resistir à degradação causada por solventes, ácidos e outros produtos químicos. É comumente utilizada em indústrias químicas e petroquímicas, onde a exposição a substâncias corrosivas é uma preocupação constante. A escolha da graxa correta para essas aplicações é fundamental para garantir a integridade dos equipamentos e a segurança dos processos.
Outro tipo de graxa que merece destaque é a graxa para rolamentos. Essa graxa é formulada especificamente para atender às necessidades de lubrificação de rolamentos, que são componentes críticos em máquinas e equipamentos. A graxa para rolamentos é projetada para proporcionar uma lubrificação eficaz, reduzindo o atrito e o desgaste, além de oferecer proteção contra a contaminação e a corrosão. A escolha da graxa adequada para rolamentos é essencial para garantir a durabilidade e o desempenho dos mesmos.
Por fim, é importante mencionar a graxa para redutores, que é utilizada em sistemas de transmissão de potência. Essa graxa é formulada para suportar altas pressões e cargas, garantindo uma lubrificação eficaz em redutores industriais. O uso de óleo para redutores industriais é fundamental para o funcionamento adequado desses sistemas, pois ajuda a minimizar o atrito e a dissipar o calor gerado durante a operação.
Em resumo, a escolha do tipo de graxa lubrificante adequada é crucial para garantir o desempenho e a durabilidade dos equipamentos. Cada tipo de graxa possui características específicas que a tornam mais apropriada para determinadas aplicações. Ao considerar as necessidades de lubrificação, é importante avaliar fatores como temperatura, ambiente de operação e tipo de equipamento para selecionar a graxa mais adequada. Com a graxa correta, é possível otimizar o funcionamento dos sistemas e prolongar a vida útil dos componentes.
Como Escolher a Graxa Lubrificante Certa para Seu Equipamento
Escolher a graxa lubrificante adequada para seu equipamento é uma tarefa fundamental que pode impactar diretamente na eficiência e na durabilidade dos componentes. A graxa correta não apenas reduz o atrito, mas também protege contra a corrosão e o desgaste, garantindo um funcionamento suave e prolongando a vida útil do equipamento. A seguir, apresentamos algumas diretrizes importantes para ajudá-lo a selecionar a graxa lubrificante ideal para suas necessidades.
O primeiro passo na escolha da graxa lubrificante é entender as especificações do equipamento que você está utilizando. Cada máquina ou componente pode ter requisitos específicos de lubrificação, que são geralmente descritos no manual do fabricante. É essencial consultar essas informações para garantir que você está utilizando o tipo de graxa recomendado. Isso inclui verificar a viscosidade, a base da graxa (sintética ou mineral) e os aditivos que podem ser necessários para a aplicação.
A viscosidade da graxa é um fator crítico a ser considerado. A viscosidade refere-se à resistência do fluido ao fluxo e é um indicador de como a graxa se comportará sob diferentes condições de temperatura e pressão. Graxas com viscosidade inadequada podem resultar em lubrificação insuficiente ou excessiva, levando a falhas no equipamento. Portanto, é importante escolher uma graxa que tenha a viscosidade adequada para a temperatura de operação do seu equipamento.
Outro aspecto importante a considerar é a base da graxa. As graxas podem ser classificadas em duas categorias principais: graxas à base de óleo mineral e graxas sintéticas. As graxas à base de óleo mineral são amplamente utilizadas e geralmente mais acessíveis. Elas são adequadas para uma variedade de aplicações, mas podem não oferecer o mesmo nível de desempenho em condições extremas que as graxas sintéticas. Por outro lado, as graxas sintéticas são formuladas para proporcionar melhor desempenho em temperaturas extremas e ambientes agressivos. Elas tendem a ter uma vida útil mais longa e oferecem maior proteção contra o desgaste. O óleo lubrificante mineral é uma opção popular para muitas aplicações, mas é importante avaliar se ele atende às necessidades específicas do seu equipamento.
Além da base e da viscosidade, os aditivos presentes na graxa também desempenham um papel importante em sua eficácia. Os aditivos podem incluir agentes antioxidantes, anticorrosivos, antidesgaste e melhoradores de aderência. Esses componentes ajudam a melhorar o desempenho da graxa em condições adversas, como altas temperaturas, umidade e exposição a produtos químicos. Ao escolher uma graxa, verifique se ela contém os aditivos necessários para a sua aplicação específica.
Outro fator a ser considerado é o ambiente em que o equipamento opera. Se o equipamento estiver exposto a condições severas, como altas temperaturas, umidade ou produtos químicos, é fundamental escolher uma graxa que seja resistente a essas condições. Por exemplo, em ambientes úmidos, uma graxa com propriedades de resistência à água é essencial para evitar a contaminação e a degradação. Em aplicações industriais, onde a exposição a produtos químicos é comum, uma graxa resistente a produtos químicos pode ser necessária para garantir a proteção adequada.
Além disso, a frequência de lubrificação também deve ser levada em conta. Equipamentos que operam em altas cargas ou em condições severas podem exigir lubrificação mais frequente. Nesse caso, é importante escolher uma graxa que tenha uma boa capacidade de retenção, para que ela permaneça no local de lubrificação por mais tempo, reduzindo a necessidade de reaplicação. Graxas com alta capacidade de retenção são especialmente úteis em aplicações onde a lubrificação regular é difícil de realizar.
Outro aspecto a considerar é a compatibilidade da graxa com os materiais do equipamento. Algumas graxas podem não ser compatíveis com certos tipos de vedação ou componentes, o que pode levar a falhas no sistema. Portanto, é importante verificar a compatibilidade da graxa com os materiais utilizados no seu equipamento antes de fazer a escolha.
Por fim, é sempre recomendável consultar um especialista em lubrificação ou um engenheiro de manutenção ao escolher a graxa lubrificante. Esses profissionais podem fornecer orientações valiosas com base em sua experiência e conhecimento sobre as melhores práticas de lubrificação para diferentes tipos de equipamentos e aplicações. Eles podem ajudar a identificar a graxa mais adequada para suas necessidades específicas e garantir que você esteja fazendo a escolha certa.
Em resumo, a escolha da graxa lubrificante certa para seu equipamento envolve considerar diversos fatores, como as especificações do fabricante, a viscosidade, a base da graxa, os aditivos, o ambiente de operação e a compatibilidade com os materiais. Ao seguir essas diretrizes e buscar a orientação de especialistas, você poderá garantir que seu equipamento funcione de maneira eficiente e duradoura, minimizando o risco de falhas e prolongando a vida útil dos componentes.
Vantagens da Utilização de Graxa Lubrificante
A utilização de graxa lubrificante é fundamental em diversas aplicações industriais e domésticas, proporcionando uma série de benefícios que garantem o bom funcionamento e a durabilidade dos equipamentos. A seguir, discutiremos as principais vantagens da utilização de graxa lubrificante e como ela pode impactar positivamente a eficiência e a vida útil dos componentes.
Uma das principais vantagens da graxa lubrificante é a redução do atrito entre superfícies móveis. O atrito excessivo pode causar desgaste prematuro, levando a falhas nos componentes e à necessidade de reparos frequentes. Ao aplicar graxa lubrificante, as superfícies são protegidas, permitindo um movimento suave e eficiente. Isso não apenas melhora o desempenho do equipamento, mas também reduz o consumo de energia, uma vez que menos energia é necessária para superar o atrito.
Além da redução do atrito, a graxa lubrificante também atua como um isolante contra a corrosão. Muitas graxas contêm aditivos anticorrosivos que protegem as superfícies metálicas da oxidação e da degradação causada pela umidade e outros agentes corrosivos. Isso é especialmente importante em ambientes industriais, onde os equipamentos estão frequentemente expostos a condições adversas. A proteção contra a corrosão ajuda a prolongar a vida útil dos componentes, reduzindo a necessidade de substituições e reparos.
A graxa lubrificante também desempenha um papel crucial na dissipação de calor. Durante a operação, os componentes geram calor devido ao atrito e à carga aplicada. A graxa ajuda a dissipar esse calor, evitando o superaquecimento e garantindo que os componentes operem dentro das temperaturas ideais. Isso é especialmente importante em aplicações de alta carga, onde o calor excessivo pode levar a falhas catastróficas. A utilização de graxa adequada, como o óleo mineral lubrificante, pode ajudar a manter a temperatura sob controle e garantir um funcionamento seguro e eficiente.
Outro benefício significativo da graxa lubrificante é a sua capacidade de vedação. A graxa forma uma barreira que impede a entrada de contaminantes, como poeira, sujeira e umidade, que podem comprometer o funcionamento dos componentes. Essa vedação é especialmente importante em ambientes industriais, onde a contaminação pode ser um problema constante. Ao manter os contaminantes fora, a graxa lubrificante ajuda a garantir que os componentes permaneçam limpos e operem de maneira eficiente.
A manutenção da graxa lubrificante também é mais simples em comparação com outros métodos de lubrificação, como óleos líquidos. A graxa tende a permanecer no local de aplicação por mais tempo, reduzindo a frequência de reaplicação. Isso é particularmente vantajoso em aplicações onde o acesso aos componentes é difícil ou onde a lubrificação regular é um desafio. A utilização de graxa lubrificante pode, portanto, resultar em menos tempo de inatividade e maior eficiência operacional.
Além disso, a graxa lubrificante pode ser formulada para atender a necessidades específicas de aplicações. Existem diferentes tipos de graxas, como graxas de alta temperatura, graxas resistentes à água e graxas para ambientes agressivos, que podem ser escolhidas com base nas condições de operação. Essa personalização permite que os usuários selecionem a graxa mais adequada para suas necessidades, garantindo um desempenho ideal e proteção adequada para os componentes.
A utilização de graxa lubrificante também contribui para a sustentabilidade. Ao prolongar a vida útil dos equipamentos e reduzir a necessidade de reparos e substituições, a graxa ajuda a minimizar o desperdício de recursos. Além disso, a redução do consumo de energia devido à diminuição do atrito também contribui para a eficiência energética, o que é benéfico tanto para o meio ambiente quanto para os custos operacionais.
Por fim, a graxa lubrificante pode melhorar a segurança operacional. Equipamentos bem lubrificados funcionam de maneira mais eficiente e confiável, reduzindo o risco de falhas inesperadas que podem levar a acidentes. A manutenção adequada da lubrificação é, portanto, uma parte essencial da gestão de segurança em ambientes industriais e comerciais.
Em resumo, a utilização de graxa lubrificante oferece uma série de vantagens significativas, incluindo a redução do atrito, proteção contra corrosão, dissipação de calor, vedação contra contaminantes, facilidade de manutenção, personalização para aplicações específicas, sustentabilidade e melhoria da segurança operacional. Ao escolher a graxa adequada e aplicá-la corretamente, é possível garantir o desempenho ideal dos equipamentos e prolongar sua vida útil, resultando em operações mais eficientes e econômicas.
Dicas para Armazenamento e Manutenção da Graxa Lubrificante
O armazenamento e a manutenção adequados da graxa lubrificante são essenciais para garantir sua eficácia e prolongar a vida útil dos equipamentos. A seguir, apresentamos algumas dicas valiosas para o armazenamento e a manutenção da graxa lubrificante, ajudando você a maximizar seu desempenho e a evitar problemas futuros.
Primeiramente, é importante armazenar a graxa em um local fresco e seco, longe da luz solar direta e de fontes de calor. A exposição a temperaturas extremas pode afetar a consistência e a eficácia da graxa, levando à degradação de seus componentes. Idealmente, a temperatura de armazenamento deve ser mantida entre 10°C e 30°C. Além disso, evite armazenar a graxa em locais onde possa ser exposta a umidade, pois isso pode causar contaminação e comprometer suas propriedades lubrificantes.
Outro aspecto importante é a escolha do recipiente adequado para o armazenamento da graxa. Utilize recipientes hermeticamente fechados e apropriados para o tipo de graxa que você está utilizando. Os recipientes devem ser limpos e livres de contaminantes antes de serem preenchidos com graxa. Se a graxa for armazenada em seu recipiente original, certifique-se de que a tampa esteja bem fechada após cada uso para evitar a entrada de umidade e sujeira.
Além disso, é fundamental rotular os recipientes de graxa com informações relevantes, como a data de fabricação, a data de validade e o tipo de graxa. Isso facilita a identificação e o controle do estoque, garantindo que você utilize a graxa dentro do prazo de validade e evitando o uso de produtos vencidos. A rotulagem adequada também ajuda a evitar confusões entre diferentes tipos de graxa, o que pode ser crucial para a manutenção correta dos equipamentos.
Quando se trata de manutenção, é importante realizar inspeções regulares nos equipamentos que utilizam graxa lubrificante. Verifique se há sinais de vazamentos, contaminação ou desgaste nos componentes. A detecção precoce de problemas pode evitar falhas maiores e custos de reparo elevados. Se você notar qualquer anomalia, como ruídos estranhos ou aquecimento excessivo, é recomendável interromper a operação do equipamento e realizar uma análise mais detalhada.
A frequência de lubrificação também deve ser monitorada. Equipamentos que operam em condições severas ou que estão sujeitos a altas cargas podem exigir lubrificação mais frequente. Consulte o manual do fabricante para determinar a frequência recomendada de lubrificação e siga essas diretrizes. A aplicação de graxa na frequência correta ajuda a garantir que os componentes permaneçam bem lubrificados e protegidos contra o desgaste.
Ao aplicar a graxa, utilize as ferramentas adequadas, como pistolas de graxa ou aplicadores, para garantir uma distribuição uniforme. Evite a aplicação excessiva de graxa, pois isso pode levar ao acúmulo de resíduos e à contaminação. A quantidade ideal de graxa deve ser suficiente para cobrir as superfícies móveis sem causar extravasamento. A aplicação correta não apenas melhora a eficiência, mas também reduz o desperdício de graxa.
Além disso, é importante manter um registro das atividades de lubrificação. Anote as datas em que a graxa foi aplicada, o tipo de graxa utilizada e quaisquer observações relevantes sobre o desempenho do equipamento. Esse registro pode ser útil para identificar padrões e tendências ao longo do tempo, permitindo que você faça ajustes nas práticas de lubrificação conforme necessário.
Outra dica importante é evitar a contaminação da graxa durante o manuseio. Sempre use ferramentas limpas e evite tocar na graxa com as mãos nuas, pois a sujeira e a gordura das mãos podem contaminar o produto. Se a graxa for armazenada em um recipiente aberto, utilize uma espátula ou colher limpa para retirar a quantidade necessária, evitando a introdução de contaminantes.
Por fim, ao adquirir graxa lubrificante, escolha um Fornecedor de óleo lubrificante confiável que ofereça produtos de qualidade. A qualidade da graxa é fundamental para garantir o desempenho adequado dos equipamentos. Sempre verifique as especificações do produto e escolha graxas que atendam às necessidades específicas de suas aplicações.
Em resumo, o armazenamento e a manutenção adequados da graxa lubrificante são essenciais para garantir sua eficácia e prolongar a vida útil dos equipamentos. Ao seguir essas dicas, você pode maximizar o desempenho da graxa, evitar problemas de lubrificação e garantir que seus equipamentos operem de maneira eficiente e confiável. A atenção aos detalhes no armazenamento e na aplicação da graxa é um investimento que se traduz em economia e eficiência a longo prazo.
Em conclusão, a graxa lubrificante é um elemento essencial para garantir a eficiência e a durabilidade de máquinas e equipamentos. Compreender os diferentes tipos de graxa, saber como escolher a mais adequada e reconhecer suas vantagens são passos fundamentais para otimizar o desempenho dos seus sistemas. Além disso, a adoção de práticas adequadas de armazenamento e manutenção assegura que a graxa mantenha suas propriedades e funcione de maneira eficaz ao longo do tempo. Investir na lubrificação correta não apenas melhora a operação dos equipamentos, mas também contribui para a redução de custos com manutenção e reparos, resultando em um ambiente de trabalho mais seguro e produtivo.